Workshop tool room machinery hold great significance as they work up as major as well as backup tools in manufacturing industries.
While you decide to buy the tool room machinery online, you are required to consider the respective dealing of that particular dealer, retailer or distributor with one or more showrooms. Make sure that they must carry different brands so as to broaden the selection process.
Also this gives the option to easily inspect the required products available with various metalworking shops and showrooms. To know about their specifications and related features, download several product brochures to make a better choice.
Quality control is yet another significant factor that falls under the consideration when one buys the workshop equipment from any online retailer. To keep your investment on a safer side, you can check for the option of personal pre-delivery inspection of the machinery so as to make certain its excellent quality control. This will help you to find faults at an early stage. Do check for the period of warranty that the manufacture is giving along with the product.
All the machines manufactured in workshop tool room such as Lathe Machine, Milling Machine, Air Compressor and Hot Saw Machines are set to be used in the rolling mill plants. The production is made in bulk. Also the quality of machines guarantees to withstand the problems and hard core manufacturing steps.
Sunday, June 6, 2010
Transformer – Major Component Of Steel Industries
Transformers are implemented as crucial steel industry equipments. The major role performed by these transformers is to make changes in the primary coil that automatically set the voltage of a current set in the secondary coil which is again either stepped-up or stepped-down.
Transformers are implemented to serve assistance in the major energy consuming processes that is generally followed in various steel making processes such as cogeneration, boilers, coke making, EAF steel making, sintering, rolling, reheating, iron making, casting and finishing. These industries are getting quite into the notion to buy expensive yet efficient transformers as even if the initial purchase cost is set high still they perform brilliantly to save the future energy costs.
The modern and advanced models of transformers keep a check on the wastage of energy when the two respective processes namely Electric Arc Furnace as well as Basic Oxygen Furnace is carried out in the rolling mills. Without transformers, the method of using alternating current for distributing power is set almost impossible.
Today, with the newer and better production techniques being introduced, the steel industries are recording the need to have more of customized transformers for their use. A certain set of specialized transformers are set in travel converters. Transformers are widely seen transporting energy from power plants to consumers which has thus made it possible to supply power to long distances.
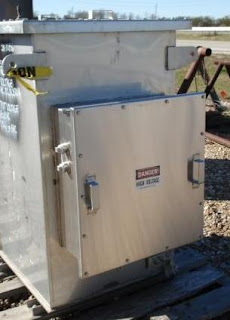
The modern and advanced models of transformers keep a check on the wastage of energy when the two respective processes namely Electric Arc Furnace as well as Basic Oxygen Furnace is carried out in the rolling mills. Without transformers, the method of using alternating current for distributing power is set almost impossible.
Today, with the newer and better production techniques being introduced, the steel industries are recording the need to have more of customized transformers for their use. A certain set of specialized transformers are set in travel converters. Transformers are widely seen transporting energy from power plants to consumers which has thus made it possible to supply power to long distances.
Industrial Shed – The Protection Shield
Industrial sheds have gained great lot of importance in industries these days. These sheds are commonly used as a protection tool in manufacturing industries.
Commonly counted types among these sheds are the metal sheds that have a great lot of variety and diversity included in their designs. These sheds are built as per latest specifications so as to offer superior guard that too for extended period of time.
Talking specifically about the metal shed, it can be said that they look similar to wooden sheds take up the core construction metals such as steel, aluminum, iron, etc. These materials make these sheds look strong and sturdy. Even the old sheds of metal are believed to last longer than the wooden sheds. Also, for this reason they are commonly used to serve protection in garages.
Construction of new shed demands a lot of expertise as well as great technical know-how that make these sheds as quality additions. These Industrial sheds are seen employed in various major sectors like in agriculture, commerce, factories and industrial. They are used in other domestic applications as well and secure stored belongings. However, metal sheds are prone to rust so application of paint saves it from getting damaged even it is set one for a longer time period.
Commonly counted types among these sheds are the metal sheds that have a great lot of variety and diversity included in their designs. These sheds are built as per latest specifications so as to offer superior guard that too for extended period of time.
Talking specifically about the metal shed, it can be said that they look similar to wooden sheds take up the core construction metals such as steel, aluminum, iron, etc. These materials make these sheds look strong and sturdy. Even the old sheds of metal are believed to last longer than the wooden sheds. Also, for this reason they are commonly used to serve protection in garages.
Construction of new shed demands a lot of expertise as well as great technical know-how that make these sheds as quality additions. These Industrial sheds are seen employed in various major sectors like in agriculture, commerce, factories and industrial. They are used in other domestic applications as well and secure stored belongings. However, metal sheds are prone to rust so application of paint saves it from getting damaged even it is set one for a longer time period.
Induction furnace - Info, Parts
A steel induction furnace is an electrical furnace that performs the task of melting in the big manufacturing industries.
In the operation of induction furnace, heat is directly made to pass through an induction heating in a conductive medium which commonly a metal. During the process of heating, a crucible is made to place in water-cooled alternating current along with a solenoid coil. The products are heated in the ind
uction furnace with the help of an electrically conducting object by passing an electromagnetic induction.
These induction furnaces are set quite clean and work as energy-efficient devices. The heating process carried on is set well-controllable. Also, the melting process carried is comparably safe as compared to the other means of metal melting.
There are many reasons why induction furnaces are being widely used as a replacement for cupolas. One reason being these induction furnace parts are more eco-friendly. This is used to melt cast iron and do not emit a lot of dust along which saves the environment from harmful pollutants.
Each induction furnace has got varied capacity that ranges less than one kilogram to a hundred ton. In manufacturing industries, major function of these furnaces is to melt aluminum, iron and steel, copper, along with other precious metals. Induction furnace is thus a significant plant settled in the cold rolling mills and smoothen the production processes.
In the operation of induction furnace, heat is directly made to pass through an induction heating in a conductive medium which commonly a metal. During the process of heating, a crucible is made to place in water-cooled alternating current along with a solenoid coil. The products are heated in the ind
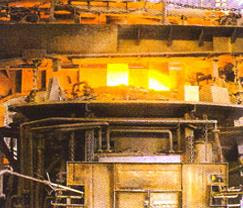
These induction furnaces are set quite clean and work as energy-efficient devices. The heating process carried on is set well-controllable. Also, the melting process carried is comparably safe as compared to the other means of metal melting.
There are many reasons why induction furnaces are being widely used as a replacement for cupolas. One reason being these induction furnace parts are more eco-friendly. This is used to melt cast iron and do not emit a lot of dust along which saves the environment from harmful pollutants.
Each induction furnace has got varied capacity that ranges less than one kilogram to a hundred ton. In manufacturing industries, major function of these furnaces is to melt aluminum, iron and steel, copper, along with other precious metals. Induction furnace is thus a significant plant settled in the cold rolling mills and smoothen the production processes.
Electric Arc Furnace - Information, Parts
An electric arc is these days employed in industries and thus serve great assistance in bulk steel manufacturing. The process carried by an electric arc furnace is similar to an oxygen route as it does not implement use of hot metal.
The modern electric arc furnace carries a typical size of 150 tons and takes up a maximum time of 90 minutes to perform the expected mel
ting process. There are two types of arc furnaces namely direct and indirect arc furnaces. Direct arc furnace has three electrodes and is used to heat metal by the way of arc. On the other hand, the indirect arc furnaces take one electrode into use and works in the same way as the direct arc furnaces do.
Steel making done in this electric arc furnace is also proven to be quite inexpensive. The Arc furnace is charged with "cold" material which is known as steel scrap. If not processed, it is prone to look like unsightly as well as environmentally damaging.
The process of carrying the process in the arc furnace starts with tipping the steel scrap. This is done using an overhead crane. Following this, a lid is place over the electric arc furnace. The lid comprises of three graphite electrodes which are kept lowered in the furnace. Following this, the electric current is made to pass through the electrodes that further help in the formation of arc. The heat generated using this arc is greatly helpful in melting the scrap.
Moving ahead in the process, some other metals like (ferro-alloys) are also added to the steel to give the product to pack it in the desired chemical composition. Just with this, oxygen is passed from the electric arc furnace so as purify the steel.
The modern electric arc furnace carries a typical size of 150 tons and takes up a maximum time of 90 minutes to perform the expected mel

Steel making done in this electric arc furnace is also proven to be quite inexpensive. The Arc furnace is charged with "cold" material which is known as steel scrap. If not processed, it is prone to look like unsightly as well as environmentally damaging.
The process of carrying the process in the arc furnace starts with tipping the steel scrap. This is done using an overhead crane. Following this, a lid is place over the electric arc furnace. The lid comprises of three graphite electrodes which are kept lowered in the furnace. Following this, the electric current is made to pass through the electrodes that further help in the formation of arc. The heat generated using this arc is greatly helpful in melting the scrap.
Moving ahead in the process, some other metals like (ferro-alloys) are also added to the steel to give the product to pack it in the desired chemical composition. Just with this, oxygen is passed from the electric arc furnace so as purify the steel.
Concast Plant - Concast furnace, Parts
Concast plant in simple words can be defined as a structure that is sued to conduct the process in which the steel is melted and is transferred to a water-cooled copper so as mould the liquid steel into solid steel billet, bloom or slab.
This process has gained a lot of room as it saves fuel along with the electrical energy, thus serving a huge capital investment. This saved amount can be further used in various interim processes like primary reheating furnace and rolling mills. This way the concast plant comes
of a great helpful to boost the overall yield and productivity. The Concast plant speed can be adjusted as per the need. It is also instilled with dust collecting bags to make sure that the manufacturing is pure and dirt free.
Also, the products obtained with the help of this manufacturing process are set more homogeneous. The process of continuous casting carried on in the concast furnace greatly helps in steelmaking operation or in ladle metallurgy that is sent directly to the semi-finished shapes so as to obtain ultimate industrial products. Further the process involves casting the molten steel straight-away in the semi-finished shapes. With the help of this way of manufacturing some important steps are set eliminated that are otherwise involved with traditional way of casting. Such process of continuous casting helps to pep up the yield along with the product quality.
The casting process is these days carried out by maximum section of industries as it gives out tremendous savings for time, labor, energy and capital.
This process has gained a lot of room as it saves fuel along with the electrical energy, thus serving a huge capital investment. This saved amount can be further used in various interim processes like primary reheating furnace and rolling mills. This way the concast plant comes

Also, the products obtained with the help of this manufacturing process are set more homogeneous. The process of continuous casting carried on in the concast furnace greatly helps in steelmaking operation or in ladle metallurgy that is sent directly to the semi-finished shapes so as to obtain ultimate industrial products. Further the process involves casting the molten steel straight-away in the semi-finished shapes. With the help of this way of manufacturing some important steps are set eliminated that are otherwise involved with traditional way of casting. Such process of continuous casting helps to pep up the yield along with the product quality.
The casting process is these days carried out by maximum section of industries as it gives out tremendous savings for time, labor, energy and capital.
Subscribe to:
Posts (Atom)